How to Determine the Thickness of Plastic Packaging Bags
The thickness of plastic packaging bags plays a crucial role in determining the protection, durability, cost-efficiency, and overall performance of the packaging. Selecting the appropriate thickness is essential for maintaining product integrity, especially when dealing with food, chemicals, pharmaceuticals, or consumer goods.
Thicker plastic bags typically provide more strength and barrier properties, but they also cost more and can be less flexible. Conversely, thinner bags are often more cost-effective but may not offer adequate protection or durability.
Determining the ideal thickness involves striking a balance between product safety, transportation logistics, customer satisfaction, and environmental impact. In this article, we will discuss the factors that influence the determination of plastic bag thickness, and how manufacturers like Kexin Packaging approach this critical decision.
1. Understanding Thickness of Plastic Packaging Bags
Plastic bag thickness is usually measured in mils or microns. A mil is equal to one-thousandth of an inch (0.001 inches), while a micron is one-thousandth of a millimeter (0.001 millimeters). For example, a 2-mil thick plastic bag is equivalent to 50.8 microns. Common packaging bags can vary from as thin as 0.5 mil to 6 mils or more, depending on their intended use.
The appropriate thickness for a plastic packaging bag is influenced by several factors, including:
- Product weight and volume
- Barrier requirements
- Handling and shipping conditions
- Environmental concerns
- Cost considerations
2. Product Characteristics
One of the most important considerations in determining plastic bag thickness is the nature of the product being packaged. Products with different weights, sizes, shapes, and fragility levels require specific thicknesses to ensure proper protection.
a. Product Weight and Density
Heavier products generally require thicker bags to prevent punctures, tears, or breakage during handling and transportation. For instance, bulk products like grains, pet food, or construction materials typically need thicker plastic bags for adequate support.
For lighter items such as clothing, lightweight food items, or small consumer goods, thinner bags may suffice as the risk of tearing or puncturing is lower.
Kexin Packaging, known for its diverse range of solutions, customizes bag thickness based on the weight and physical demands of the product. For instance, heavier products like liquids or sharp-edged items may require bags with a thickness of 4 mils or more, while light, dry items may be safely packaged in thinner bags, around 1 or 2 mils.
b. Fragile or Sharp Items
For items with sharp edges or fragile components, thicker plastic is recommended to prevent damage to both the bag and the product. Packaging fragile products such as electronics, glass, or delicate food products requires thicker bags to provide a cushion and resist punctures. Double-layer or reinforced bags are sometimes used for added protection.

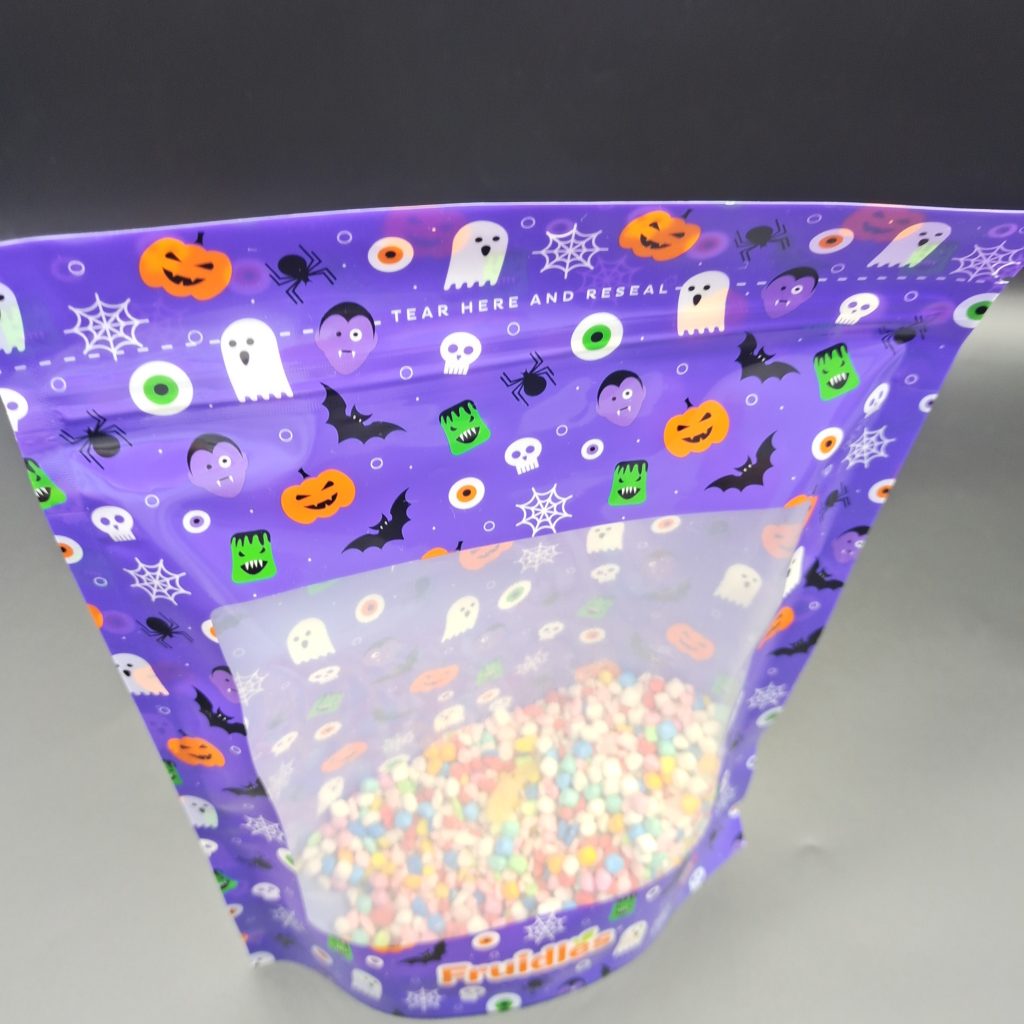
3. Barrier Requirements
The barrier properties required to protect the product from external factors such as moisture, oxygen, light, or contamination are another crucial consideration when determining thickness.
a. Moisture and Oxygen Sensitivity
Products that are sensitive to moisture and oxygen degradation, like food, pharmaceuticals, or certain chemicals, require packaging with strong barrier properties. Thicker plastic typically provides better resistance to permeation, keeping the product fresher for longer. Multilayer plastic structures, which may include barrier materials like EVOH or nylon, can also be incorporated to improve resistance while keeping the outer plastic layer relatively thin.
For example, Kexin Packaging often combines multiple layers of thin plastic films with high-barrier materials to provide superior protection without significantly increasing the overall thickness. This method ensures that products like sauces, processed foods, and pet foods remain fresh for extended periods.
b. Light and UV Sensitivity
Certain products, particularly food and pharmaceutical items, may be sensitive to light or UV exposure, which can cause degradation over time. Thicker bags or additional layers may be necessary to shield such products from harmful light exposure. If light sensitivity is a concern, materials like metallized films or aluminum coatings are sometimes used in combination with thicker plastic layers for optimal protection.
4. Handling and Shipping Conditions
The conditions under which a packaged product will be transported, handled, and stored also influence the selection of plastic thickness.
a. Transport and Storage
If a product is expected to go through a rigorous distribution chain, with exposure to rough handling, stacking, or fluctuating temperatures, thicker bags are needed to protect the integrity of the product. For long shipping distances, especially for export, packaging must be sturdy enough to endure vibration, pressure, and potentially harsh environmental conditions.
Thicker bags are less likely to tear or puncture, which is especially important for products that are stored or shipped in bulk. On the other hand, thinner plastic bags may work well for short-distance shipping or controlled environments where the risk of physical damage is lower.
Kexin Packaging addresses these logistics considerations by evaluating the product’s handling conditions and selecting the ideal thickness to optimize durability while maintaining cost-efficiency.
5. Environmental Considerations
The environmental impact of packaging materials has become an increasingly important factor in the decision-making process. Thicker plastic bags often use more raw materials, which can contribute to a higher carbon footprint. However, using thicker, more durable materials can reduce the need for additional protective packaging, such as secondary boxes or fillers, thereby balancing environmental concerns.
a. Sustainable Materials
With advancements in biodegradable and recyclable plastic materials, companies like Kexin Packaging are finding ways to offer eco-friendly alternatives without compromising the required thickness for protection. These sustainable options are particularly attractive for industries looking to reduce their environmental footprint while still meeting performance standards.
b. Down-Gauging
Down-gauging is the process of reducing the thickness of the plastic material while maintaining or improving its strength and barrier properties. This is achieved through the use of advanced polymers and manufacturing technologies. Kexin Packaging incorporates down-gauging techniques to help reduce material usage and environmental impact, offering thinner but equally effective plastic bags for various applications.
6. Cost Considerations
Finally, the cost of the packaging material is a key factor when determining thickness. Thicker plastic generally costs more due to the additional material and potential shipping expenses associated with the increased weight. However, selecting thinner material without compromising product safety and durability can lead to significant savings.
Kexin Packaging works closely with clients to find the ideal thickness that balances performance and cost. By evaluating the specific requirements of each product, Kexin Packaging ensures that manufacturers get the most cost-effective solution without sacrificing quality.
Conclusion
Determining the thickness of plastic packaging bags is a complex decision influenced by product characteristics, barrier requirements, handling conditions, environmental concerns, and cost. Companies like Kexin Packaging use a combination of factors to customize the perfect solution for each product, ensuring that the packaging is durable, protective, and cost-effective. Whether it’s lightweight products or sensitive materials requiring high-barrier protection, the right thickness can make all the difference in ensuring product safety and consumer satisfaction.
You can visit our website to know more about our flexible packaging pouch: