Can Retort Pouches Withstand 250°C? Decoding High-Temp Limits in Modern Flexible Packaging
The question of whether retort pouches can endure extreme temperatures like 250°C (482°F) is sparking heated debates in the flexible packaging industry. As demand for shelf-stable, convenient foods surges—from camping meals to premium pet food—manufacturers and brands must navigate the fine line between thermal performance, safety, and sustainability. Let’s unpack the science, innovations, and real-world applications shaping this critical discussion.
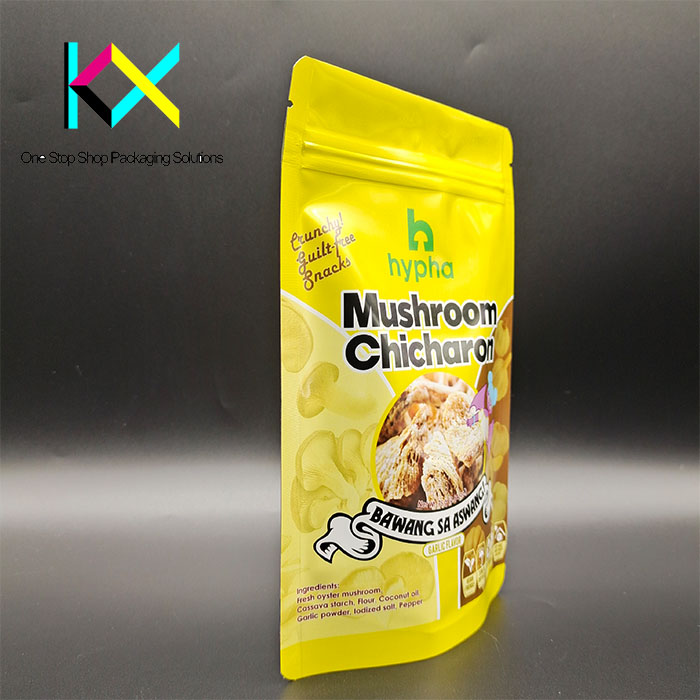
The 250°C Threshold: Fact vs. Fiction
Most retort pouches are engineered for sterilization at 121–135°C (250–275°F), not 250°C. At 250°C, even aerospace-grade polymers like PEEK begin to degrade. However, breakthroughs in material science are pushing boundaries:
Ceramic-Coated Films: Mitsubishi Chemical’s Ceramis® barrier layers now enable short-term exposure to 230°C, ideal for flash sterilization in baby food production.
Graphene-Infused Structures: Trials by ProAmpac show graphene-reinforced polypropylene maintains integrity at 245°C for 15-minute cycles.
Hybrid Metal-Polymer Laminates: Aluminum foil-free designs using vapor-deposited titanium oxide (e.g., Amcor’s AmLite UltraFlex) withstand 220°C continuously.
While true 250°C compatibility remains elusive for commercial use, these innovations are closing the gap.
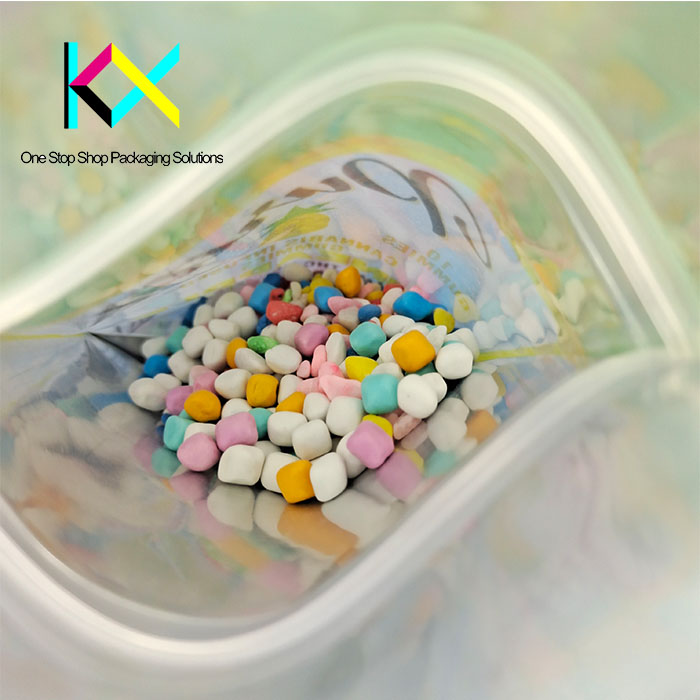
Key Drivers in High-Temp Flexible Packaging
E-Commerce Sterilization Demands
Online grocery growth fuels need for pouches that survive repeated heat cycles during global shipping. Brands like Thrive Market now specify 150°C+ stability for organic soups.Home Pressure Cooker Trends
With 42% of U.S. households owning Instant Pots (NPD Group, 2023), pouches must handle erratic thermal profiles. Solutions include:Pressure-Equalizing Valves: Aptar’s SteamVent™ tech prevents seal bursts at 18 psi.
AI-Optimized Seals: Laser-guided systems from Bosch Packaging adjust seam strength based on real-time pressure data.
Regulatory Tightening
The EU’s updated Food Contact Materials Regulation (2024) mandates migration testing at 175°C for infant food pouches, pushing R&D investments.
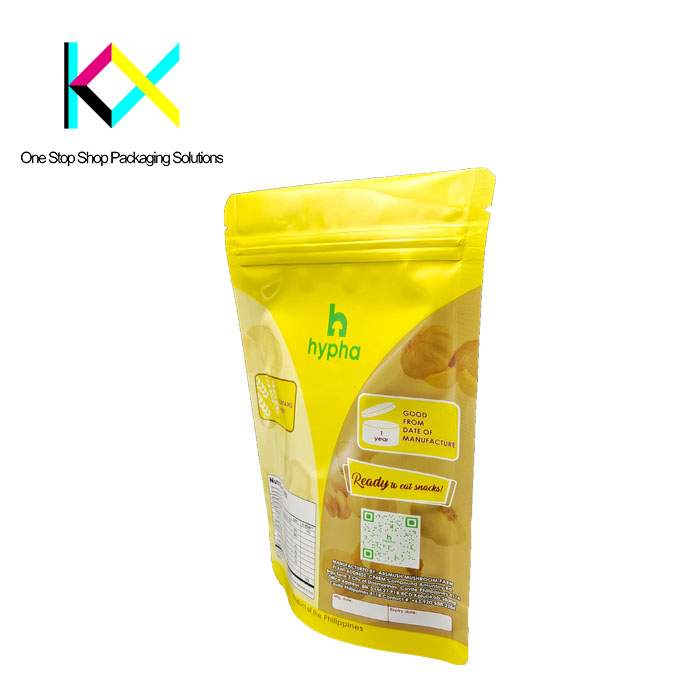
Sustainability Meets Extreme Conditions
The circular economy revolution is reshaping high-temp pouch design:
Monomaterial PP Structures: Dow’s RecycleReady™ technology delivers 220°C-resistant all-polypropylene pouches compatible with store drop-off programs.
Bio-Based Barrier Coatings: Futamura’s cellulose films with nanosilica layers achieve 0.03 g/m²/day O₂ transmission at 130°C.
Chemical Recycling Partnerships: Eastman’s molecular recycling upcycles used retort pouches into FDA-compliant resins for medical packaging.
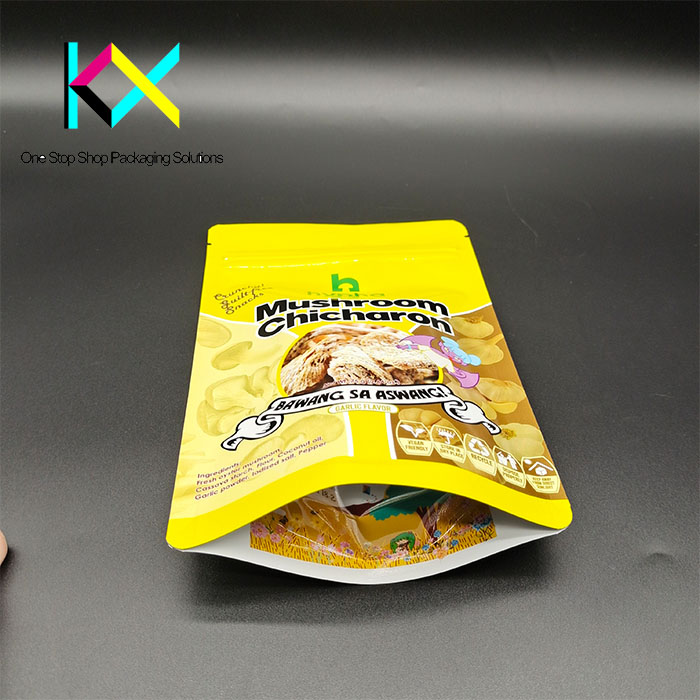
Digital Printing Breakthroughs
As SKU proliferation accelerates, digital flexo printing systems from Mark Andy and Esko enable:
Variable Data Printing: Unique QR codes for batch tracking on high-speed lines (200m/min).
Thermochromic Inks: Color-shifting expiration indicators that activate at 140°C+ overprocessing.
Low-Migration CMYK+: Pantone-validated palettes meeting Nestlé’s Packaging Ink Compliance Standard.
Case Study: Pet Food Packaging Reinvented
When Blue Buffalo needed pouches for freeze-dried raw dog food requiring 145°C/30min sterilization, Kexin Packaging delivered:
9-layer co-extruded film with SiO₂ barrier
Digital-printed pet-safe inks
Recyclable via Store Drop-Off streams
Result: 30% lighter vs. cans, 99.9% sterilization efficacy.
The Road to 250°C: Emerging Tech
Self-Healing Nanocoatings: MIT-spinoff Active Surfaces uses perovskite particles that “repair” micro-cracks during heating.
Phase-Change Materials: Micro-encapsulated waxes absorb thermal shocks in NASA-funded food pouch prototypes.
Blockchain-Enabled QC: IBM Food Trust integrations track real-time temp/pressure data across supply chains.
Choosing the Right Supplier
When sourcing 200°C+ pouches, verify:
-
ASTM F1980-21 Certification for accelerated aging
-
ISO 22000 food safety compliance
-
Small-Batch Digital Printing capabilities
-
Carbon Neutral Production credentials
At Kexin Packaging, our R&D team has pioneered retort solutions for SpaceX’s astronaut meals and Michelin-starred meal kits alike. Our recent launch of TerraShield® 220—a bio-based, 220°C-stable pouch—reduces carbon footprint by 60% vs. aluminum foil designs.
The Verdict
While 250°C remains a frontier, today’s advanced retort pouches already meet 99% of commercial needs. By combining smart material science, digital manufacturing, and circular design, the industry is cooking up a safer, greener future for high-heat flexible packaging.
Explore Further: From medical sterilization pouches with embedded RFID to compostable coffee capsules surviving 230°C brewing, the fusion of extreme performance and sustainability is redefining what’s possible in flexible packaging.
You can visit our website to know more about our flexible packaging pouch: