How to Test the Seal Integrity of Flexible Plastic Packaging: A Focus on Digital Printing
Flexible plastic packaging plays a crucial role in protecting products from external factors like moisture, air, light, and contaminants. Whether it’s for food, pharmaceuticals, or consumer goods, the integrity of the seal is vital for preserving the freshness, safety, and quality of the product inside. Proper sealing not only ensures that the packaging performs its protective function, but also maintains brand credibility and consumer trust. In this article, we will explore various methods to test the seal integrity of flexible plastic packaging, with a particular emphasis on how digital printing technology interacts with the sealing process and contributes to the packaging’s overall functionality.
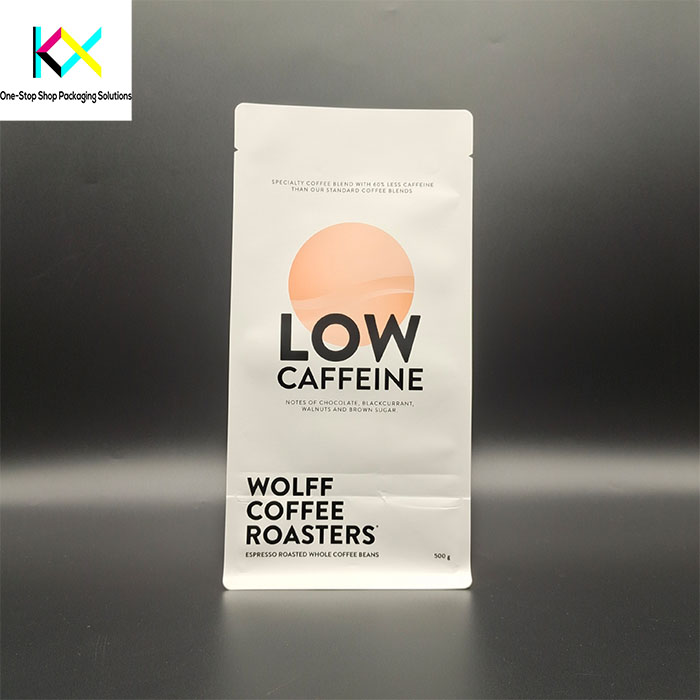
1. Importance of Seal Integrity in Flexible Plastic Packaging
Seal integrity is one of the most important factors in the overall performance of flexible plastic packaging. If the seal fails, the package can no longer protect its contents from moisture, oxygen, or contaminants. This can result in the degradation of the product, leading to spoilage, loss of quality, or even contamination. For products like food, which are sensitive to external factors, a reliable seal is crucial for extending shelf life and ensuring consumer safety.
In addition to the protective aspects, the visual appeal of the seal is also important for branding. A clean, precise seal ensures that the packaging looks professional, which is especially important for products that are displayed on retail shelves.
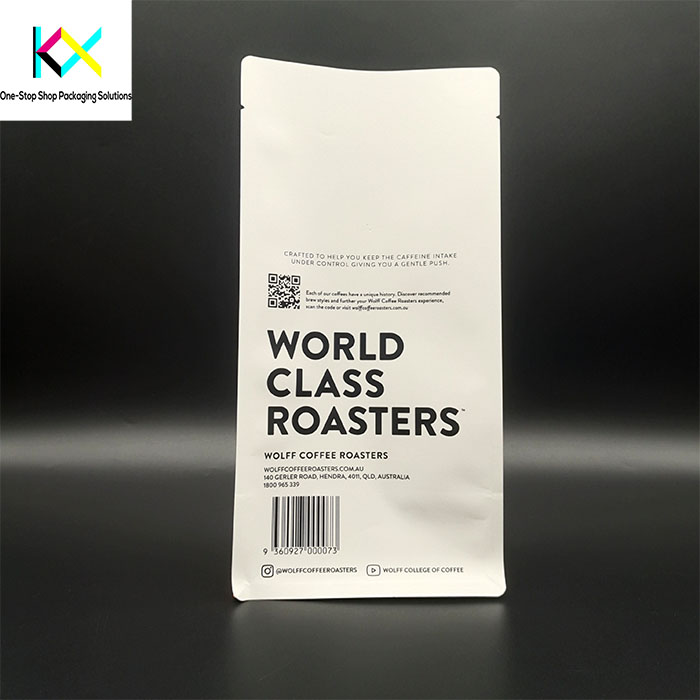
2. Methods to Test the Seal Integrity of Flexible Plastic Packaging
There are several methods used to test the seal integrity of flexible plastic packaging. These methods vary in complexity and the level of detail they provide, but all are aimed at identifying potential seal failures that could compromise the packaging’s performance.
Visual Inspection
Visual inspection is one of the simplest and most common methods for testing seal integrity. Packaging manufacturers or quality control personnel look for visible defects in the seal, such as wrinkles, incomplete seals, or gaps. A clean, consistent seal is typically a sign of a good-quality seal, while irregularities could indicate potential issues. However, visual inspection alone may not detect microscopic leaks or flaws, so it is often used in combination with other methods.
Pressure Testing
Pressure testing is a more advanced method used to test the seal integrity of flexible plastic packaging. In this test, air or gas is injected into the sealed package, and the package is subjected to increased pressure. The packaging is then checked for leaks, which would cause the internal pressure to drop. This method is particularly useful for testing vacuum-sealed or gas-flushed packaging, which is common for products like chips, snacks, or vacuum-packed meats.
One common form of pressure testing is bubble emission testing, where the package is submerged in water, and the presence of bubbles indicates a leak in the seal. This method is sensitive and can detect even the smallest leaks.
Vacuum Decay Testing
Vacuum decay testing is another highly effective method for evaluating the seal integrity of flexible plastic packaging. The packaging is placed in a vacuum chamber where the air pressure is reduced. Any leaks in the seal will allow air to flow back into the package, causing a detectable change in the vacuum level. This method is widely used for food and pharmaceutical packaging, where it is essential to maintain a controlled atmosphere inside the package.
Peel Testing
Peel testing involves applying force to the edges of the seal to determine how well the materials are bonded together. The packaging is pulled apart at the seal, and the force required to break the seal is measured. This test provides insight into the strength of the seal and whether it is strong enough to withstand handling and transportation. It is especially useful for packaging that requires tamper-evident seals or resealable pouches.
Dye Penetration Testing
Dye penetration testing involves applying a colored dye to the outside of the packaging. The packaging is then immersed in the dye solution for a period of time, and the inner seal is examined for dye penetration. If the dye seeps into the package, it indicates a breach in the seal. This method is especially useful for detecting microscopic or hard-to-find leaks.
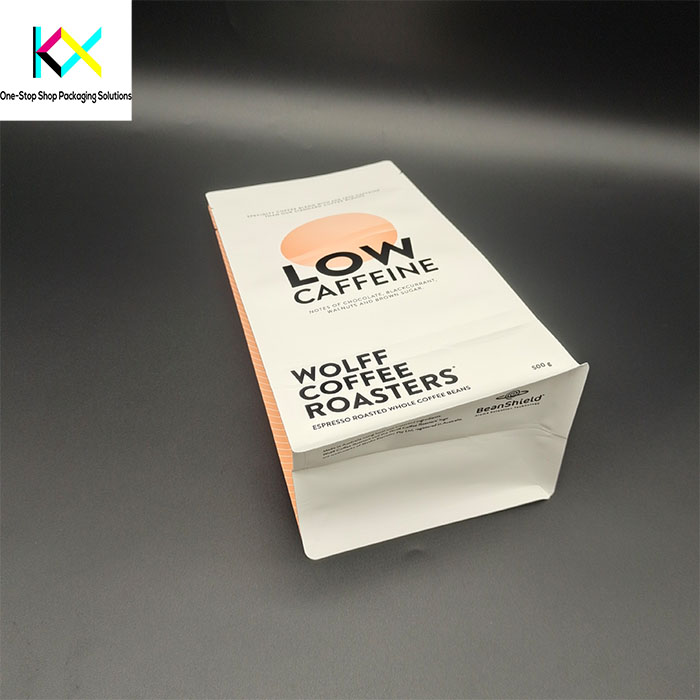
3. The Impact of Digital Printing on Seal Integrity
While the primary function of flexible plastic packaging is to protect the product, it also serves as a vital marketing tool. Digital printing technology plays a key role in enhancing the appearance and customization of packaging, but it also has an important impact on the sealing process.
Digital printing allows for high-resolution graphics, variable data, and vibrant colors to be directly printed onto flexible plastic films. This enhances the overall branding and visual appeal of the packaging. However, there are considerations to ensure that digital printing does not interfere with the sealing process.
Ink Selection and Print Placement
Digital printing requires the use of inks that are compatible with the sealing process. Some inks may interfere with the ability of the heat sealing process to create a tight bond between the materials. For instance, solvent-based inks or inks with heavy coatings may leave a residue that can weaken the seal. It’s essential to choose eco-friendly and seal-compatible inks, such as UV-cured or water-based inks, that will not hinder the heat-sealing process.
In addition, the placement of printed designs is important. Printing over areas that will be sealed can affect the bond strength. To avoid this, many manufacturers choose to keep printing away from the seal areas to ensure that the integrity of the seal is maintained.
Testing Printed Seals
For companies that use digital printing for their packaging, it is important to test not only the visual quality of the printed design but also its interaction with the seal. Any distortion or warping of the printed material near the seal line could lead to weak spots in the seal. Performing a peel test or vacuum decay test on digitally printed packages can help identify any issues early in the production process.
Customization and Branding
Digital printing also allows for the addition of security features like QR codes, batch numbers, or tamper-evident seals. These features can be integrated into the packaging design while still ensuring that the seal is secure and the packaging maintains its protective qualities. Additionally, digital printing enables customized seals, such as printing a unique seal pattern that indicates whether the package has been opened, providing an added layer of security for consumers.
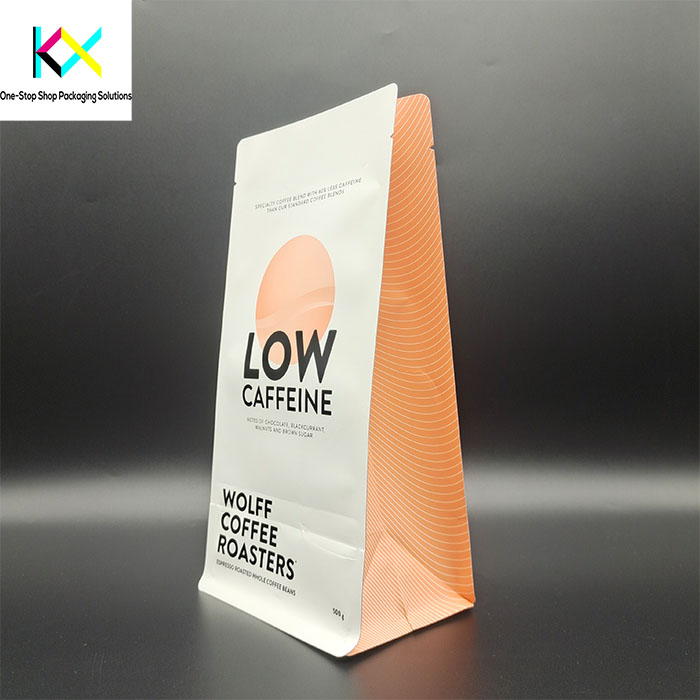
4. Conclusion
Testing the seal integrity of flexible plastic packaging is a critical step in ensuring the protection and preservation of the product inside. Methods like visual inspection, pressure testing, vacuum decay testing, peel testing, and dye penetration testing all play a role in identifying potential seal failures and ensuring that the packaging meets quality standards.
Digital printing technology enhances the design and branding of flexible plastic packaging, but it is important to consider how it interacts with the sealing process. By selecting compatible inks and ensuring that printed areas do not interfere with the seal, businesses can maintain both the aesthetic appeal and functionality of the packaging. Digital printing offers the flexibility for customization and high-quality graphics, while still supporting the primary function of the packaging—sealing and protecting the product inside.
You can visit our website to know more about our flexible packaging pouch:
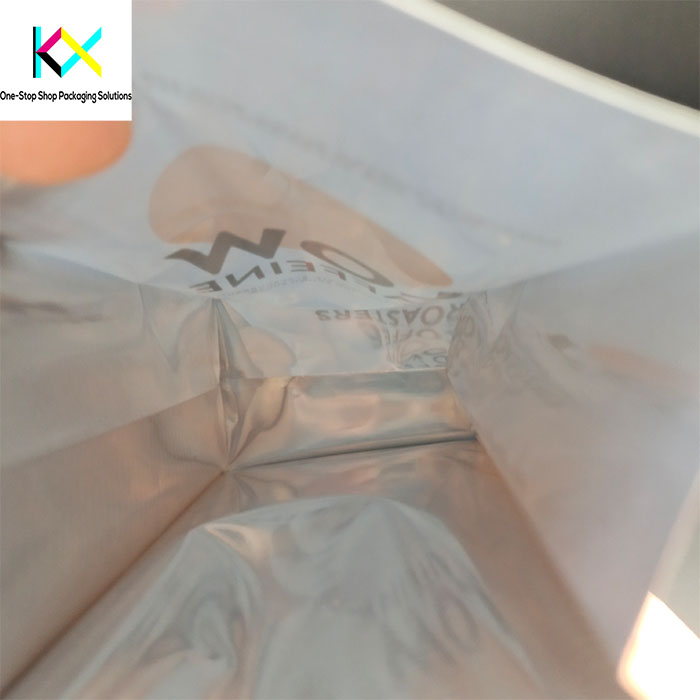