Oxygen Transmission Rate in Retort Pouches: Balancing Barrier Performance and Sustainability in Modern Flexible Packaging
In the competitive landscape of shelf-stable food packaging, oxygen transmission rate (OTR) in retort pouches has become a pivotal factor driving innovation, regulatory compliance, and consumer trust. As the global retort packaging market accelerates toward $6.8 billion by 2027, manufacturers are racing to achieve ultra-low oxygen transmission rates (≤0.5 cc/m²/day) while navigating stringent EU recycling mandates and FDA food safety standards. This delicate balance between barrier efficiency and environmental responsibility is redefining the future of high-temperature flexible packaging.
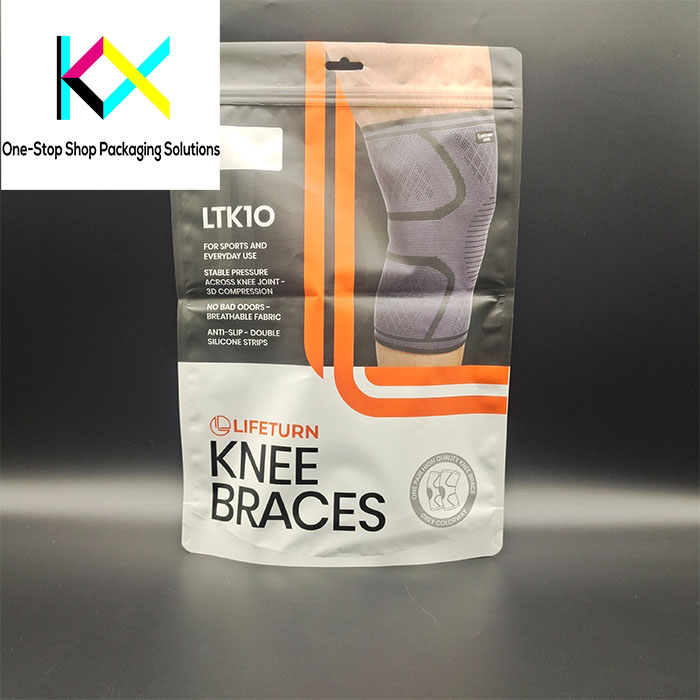
The Critical Role of OTR in Retort Packaging
Oxygen transmission rate directly dictates product shelf life, nutrient preservation, and microbial safety. Traditional aluminum foil retort pouches deliver exceptional OTR (<0.1 cc/m²/day) but face recycling challenges due to mixed-material structures. Emerging solutions now prioritize both performance and circularity:
Ceramic Nanocoating Technology
Amcor’s AmLite UltraFlex employs plasma-enhanced SiO₂ layers to achieve OTR of 0.3 cc/m²/day, replacing aluminum in 135°C-resistant pouches for brands like Nomad Nutrition.Graphene-Enhanced Films
Kureha’s G-Lam™ integrates graphene flakes into polypropylene, reducing OTR by 60% versus standard films while enabling full recyclability—a breakthrough for organic baby food packaging.Active Oxygen Scavengers
Mitsubishi’s Ageless® ZP strips absorb residual oxygen post-sterilization, maintaining OTR stability for iron-sensitive products like fortified broths.
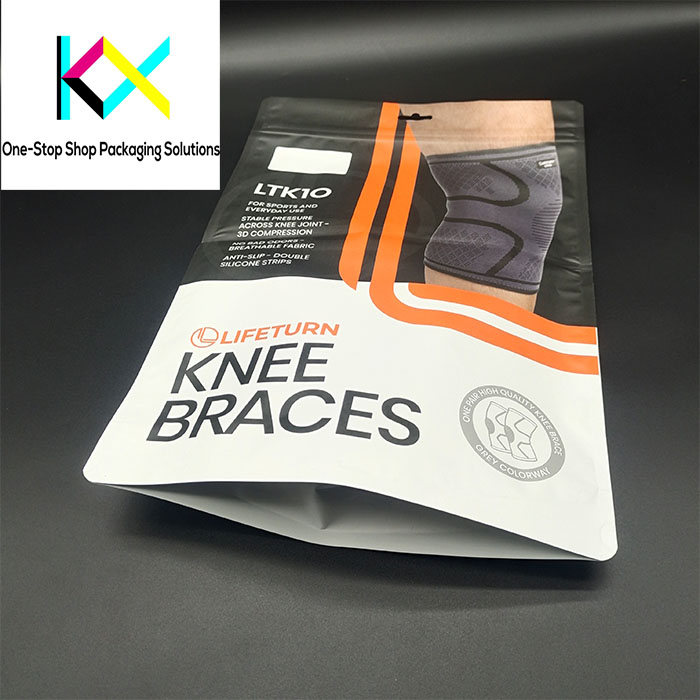

Sustainability-Driven OTR Innovations
With the EU’s Single-Use Plastics Directive (SUPD) penalizing non-recyclable designs, material scientists are reimagining oxygen transmission rate control:
Monomaterial PP Structures: Dow’s RecycleReady™ all-polypropylene pouches achieve OTR 0.8 cc/m²/day, compatible with store drop-off programs.
Chemical Recycling Integration: Eastman’s molecular recycling regenerates high-barrier retort pouches into food-grade resins without compromising OTR performance.
Bio-Based Barriers: Futamura’s cellulose films with nanosilica coatings hit OTR 1.2 cc/m²/day, meeting compostability standards for plant-based ready meals.
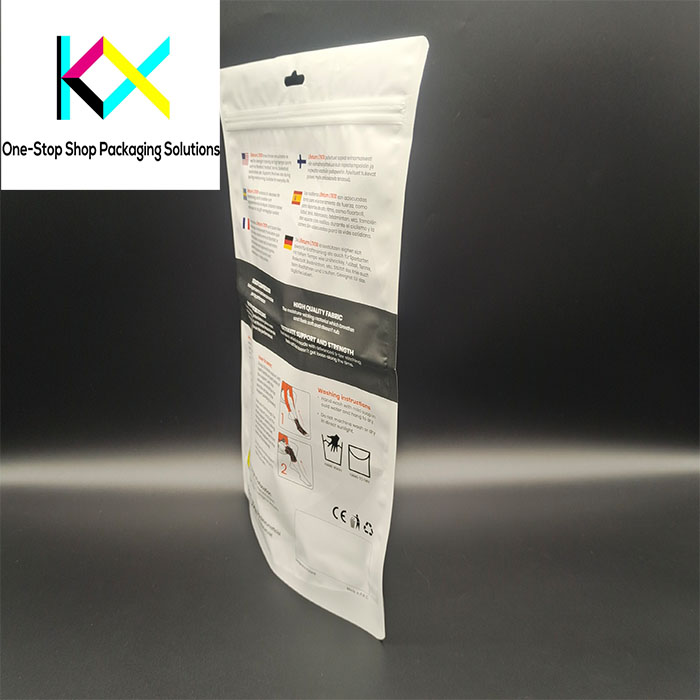
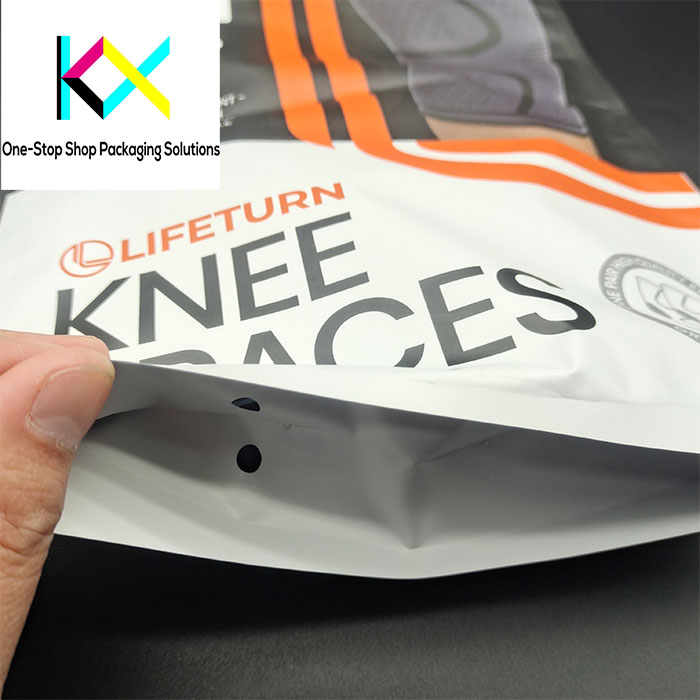
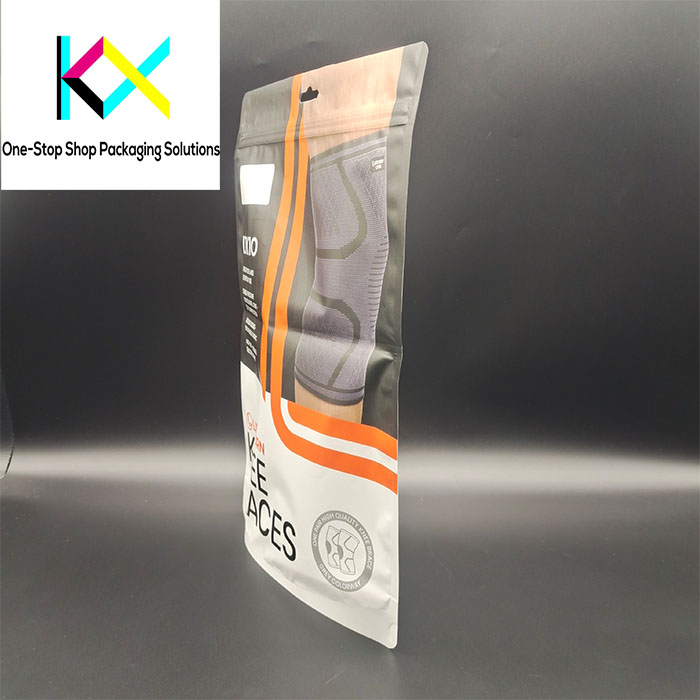
Smart Technologies Revolutionizing OTR Management
Digital advancements are transforming oxygen transmission rate precision and transparency:
IoT-Enabled Production: Bosch’s PackVis NIR systems monitor OTR variations (±0.05 cc/m²/day) in real-time at 200m/min speeds.
Blockchain Traceability: Avery Dennison’s Atma.io platform tracks OTR compliance across supply chains via NFC-enabled retort pouches.
AI-Optimized Design: BASF’s Ultrasim® software predicts OTR for custom structures, reducing prototyping time by 70%.
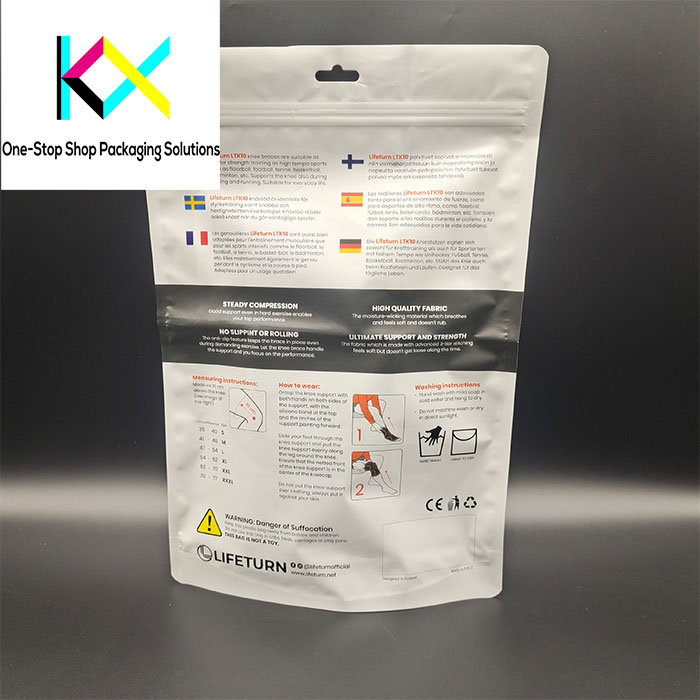
Industry Applications Setting New OTR Benchmarks
Pet Food: Blue Buffalo’s 2024 monomaterial pouches (OTR 0.6 cc/m²/day) eliminate metal detection issues in automated facilities.
Medical Nutrition: Nestlé Health Science’s Peptamen® uses OTR 0.2 cc/m²/day films with embedded RFID for real-time cold chain monitoring.
E-Commerce Meals: Factor_’s keto line employs OTR 0.4 cc/m²/day pouches surviving 48-hour ambient shipping.
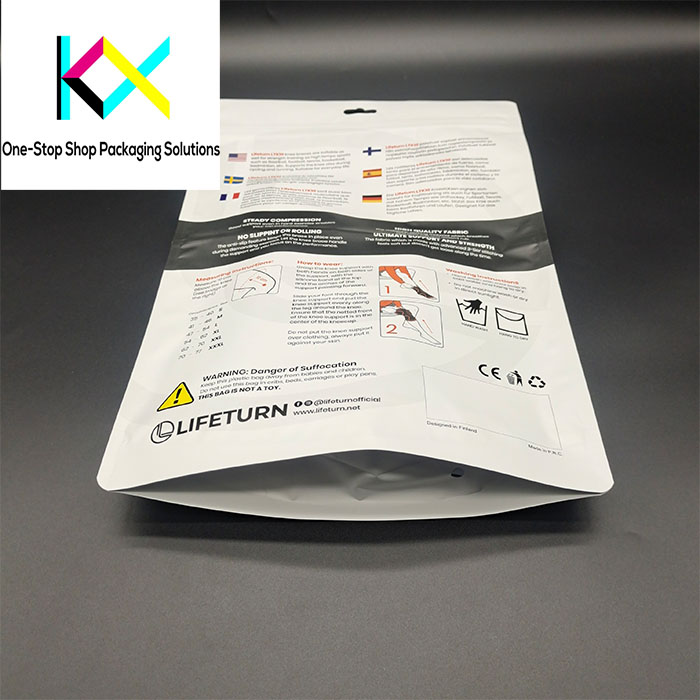
Regulatory Challenges Reshaping OTR Standards
Global compliance now demands:
Enhanced Migration Testing: FDA 21 CFR 175.300 requires additive stability validation under maximum OTR conditions.
Carbon Transparency: EU’s PPWR mandates CO₂/cc OTR reporting across packaging lifecycles.
Recyclability Grading: The HowLowCanWeGo Initiative scores pouches by OTR vs. recyclability performance.
Future Frontiers in OTR Control
Self-Healing Barriers: MIT-spinout Active Surfaces uses perovskite nanocrystals to autonomously seal micro-leaks, sustaining OTR <0.1 cc/m²/day post-sterilization.
4D-Printed Films: Stratasys’ programmable materials adjust OTR dynamically based on external humidity/temperature.
Edible Coatings: Notpla’s seaweed-based layers (OTR 2.1 cc/m²/day) target short-shelf-life condiments.
Partnering for OTR Excellence
Navigating the oxygen transmission rate landscape requires suppliers offering:
-
Multi-Layer Coextrusion Expertise
-
ASTM F1927-Certified OTR Testing
-
Small-Batch Digital Printing for customized barriers
-
Carbon-Neutral Manufacturing
At Kexin Packaging, our OTR Shield™ technology delivers 0.15 cc/m²/day performance using 100% recyclable monomaterials. Recently, we partnered with a Michelin-starred meal service to achieve 18-month shelf life with 40% less material than aluminum foil—proving that sustainability and oxygen transmission rate mastery can coexist.
The Verdict: In an era where every molecule of oxygen impacts profitability and planetary health, oxygen transmission rate isn’t just a metric—it’s the linchpin of tomorrow’s flexible packaging success.
You can visit our website to know more about our compostable pouch: